振動(dòng)分析在滑動(dòng)軸承故障診斷中的應(yīng)用
滑動(dòng)軸承是旋轉(zhuǎn)機(jī)械中應(yīng)用***廣的機(jī)械零件,也是***易損壞的元件之一?;瑒?dòng)軸承的剛度和阻尼影響著轉(zhuǎn)子的動(dòng)力特性, 其工作好壞對旋轉(zhuǎn)機(jī)械的工作狀態(tài)有很大的影響。在研究旋轉(zhuǎn)機(jī)械故障問題時(shí), 轉(zhuǎn)子的許多故障都與滑動(dòng)軸承有關(guān)?;瑒?dòng)軸承工作異常會(huì)導(dǎo)致旋轉(zhuǎn)機(jī)械產(chǎn)生異常振動(dòng)和噪聲, 甚至成旋轉(zhuǎn)件損壞。
本文通過分析滑動(dòng)軸承可能出現(xiàn)的故障類型、故障特征, 結(jié)合某渦輪增壓器試驗(yàn)中的振動(dòng)數(shù)據(jù), 來判斷該渦輪增壓器滑動(dòng)軸承出現(xiàn)的故障及其原因,并尋求解決方案。
2 滑動(dòng)軸承動(dòng)力特性、典型故障
2.1 滑動(dòng)軸承動(dòng)力特性
***簡單的軸頸滑動(dòng)軸承是由軸頸和圓柱形軸瓦組成, 叫全圓軸承。軸瓦的直徑一般比軸頸大千分之一到千分之二。當(dāng)軸頸在軸瓦中轉(zhuǎn)動(dòng)時(shí), 應(yīng)保證有足夠的潤滑油進(jìn)入軸頸和軸瓦之間的間隙中去形成油膜, 間隙中油膜的流體動(dòng)壓力使軸頸有足夠的承載能力。而循環(huán)的潤滑油又帶走軸承中摩擦產(chǎn)生的熱量, 保證軸承正常的工作溫度。
當(dāng)轉(zhuǎn)軸受到某種外來擾動(dòng)時(shí), 軸頸中心就會(huì)在靜平衡位置附近發(fā)生渦動(dòng), 此時(shí)油膜作用在軸頸上的反力就會(huì)發(fā)生變化。力的變化與擾動(dòng)之間的關(guān)系一般是非線性的, 但是當(dāng)擾動(dòng)是微小量時(shí)可以近似認(rèn)為力的變化與擾動(dòng)之間的關(guān)系是線性的。將油膜力對擾動(dòng)參數(shù)作Taylor 展開, 保留一階微量, 可得:
Fx=Fx0+Kxxx+Kxyy+Cxxx!+Cxyy!
Fy=Fy0+Kyxx+Kyyy+Cyxx!+Cyyy!
!#"#$(1)其中: Fx、Fy分別為油膜力在x、y 方向上的分量; Fx0 、Fy0
分別為平衡位置時(shí)油膜力在x、y 方向上的分量;x、y 為軸心偏離平衡位置的位移分量; x! 、y! 為軸心的速度分量; Kxx、Kxy、Kyx、Kyy
為油膜剛度系數(shù), 且有Kxx= !Fx
!x 0, Kxy= !Fx!y 0, Kyx= !Fy!x 0, Kyy= !Fy
!y 0; Cxx、Cxy、Cyx、Cyy
為油膜阻尼系數(shù), 且有Cxx= !Fx!x! 0, Cxy= !Fx
!y! 0, Cyx=!Fy!x! 0, Cyy= !Fy!y! 0。式中Kxy、Kyx、Cxy、Cyx
又稱為交叉動(dòng)力系數(shù), 其大小和正負(fù)在很大程度上影響著軸承工作的穩(wěn)定性[1]。
由式(1)得油膜力的增量, 即動(dòng)態(tài)力為:
ΔFx=Fx- Fx0=KxxΔx+KxyΔy+CxxΔx!+CxyΔy!
ΔFy=Fy- Fy0=KyxΔx+KyyΔy+CyxΔx!+CyyΔy!
!#"#$(2)令x、y 為軸頸的動(dòng)位移, fx、fy 為油膜動(dòng)態(tài)力,
剛度系數(shù)矩陣%K&=Kxx Kxy
Kyx Kyy % &, 阻尼系數(shù)矩陣%C&=Cxx Cxy
Cyx Cyy % &, 則式(2)可以寫成:fxf ’( y=%K&x ’( y+%C&x!y! ’(
(3)動(dòng)態(tài)分析時(shí)軸承的力學(xué)模型如圖1 所示。
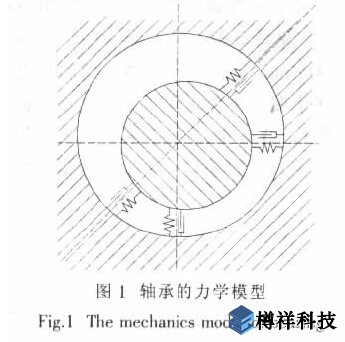
2.2 滑動(dòng)軸承典型故障
2.2.1 油膜振蕩
如前所述, 當(dāng)軸頸在外界偶然擾動(dòng)下所發(fā)生的任一偏移, 軸承油膜除了產(chǎn)生沿偏移方向的彈性恢復(fù)力以保持和外載荷平衡外, 還要產(chǎn)生一個(gè)垂直于偏移方向的切向失穩(wěn)分力, 這個(gè)失穩(wěn)分力會(huì)驅(qū)動(dòng)轉(zhuǎn)子作渦動(dòng)運(yùn)動(dòng), 當(dāng)阻尼力大于切向失穩(wěn)分力時(shí), 這種渦動(dòng)是收斂的, 即軸頸在軸承內(nèi)的轉(zhuǎn)動(dòng)是穩(wěn)定的; 當(dāng)切向失穩(wěn)分力大于阻尼力時(shí), 渦動(dòng)是發(fā)散的, 軸頸的運(yùn)動(dòng)是不穩(wěn)定的, 油膜振蕩就是這種情況。介于兩者之間的渦動(dòng)軌跡為封閉曲線, 半速渦動(dòng)就是這種情況。
轉(zhuǎn)軸的轉(zhuǎn)動(dòng)在失穩(wěn)轉(zhuǎn)速以前是平穩(wěn)的, 當(dāng)達(dá)到失穩(wěn)轉(zhuǎn)速后即發(fā)生半速渦動(dòng)。隨著轉(zhuǎn)速升***, 渦動(dòng)角速度也將隨著增加, 但總保持著約等于轉(zhuǎn)動(dòng)速度一半的比例關(guān)系, 半速渦動(dòng)一般并不劇烈。當(dāng)轉(zhuǎn)軸轉(zhuǎn)速升到比***階臨界轉(zhuǎn)速的2 倍稍***以后, 由于此時(shí)半速渦動(dòng)的渦動(dòng)速度與轉(zhuǎn)軸的***階臨界轉(zhuǎn)速相重合即產(chǎn)生共振, 表現(xiàn)為強(qiáng)烈的振動(dòng)現(xiàn)象, 稱為油膜振蕩。
油膜振蕩一旦發(fā)生, 就將始終保持約等于轉(zhuǎn)子一階臨界轉(zhuǎn)速的渦動(dòng)頻率, 而不再隨轉(zhuǎn)速的升***而升***。
文獻(xiàn)[2]指出, 油膜振蕩故障具有以下特征:
(1) 油膜振蕩總是發(fā)生在轉(zhuǎn)速***于轉(zhuǎn)子系統(tǒng)一階臨界轉(zhuǎn)速的2 倍以上。
(2) 油膜振蕩的頻率接近轉(zhuǎn)子的一階臨界轉(zhuǎn)速, 即使轉(zhuǎn)速再升***, 其頻率也基本不變。
(3) 油膜振蕩時(shí), 轉(zhuǎn)子的撓曲呈一階振型。
(4) 油膜振蕩時(shí), 轉(zhuǎn)子渦動(dòng)方向與轉(zhuǎn)子轉(zhuǎn)動(dòng)方向相同, 軸心軌跡呈花瓣形, 正進(jìn)動(dòng)。
(5) 軸承載荷越小或偏心率越小, 越易發(fā)生油膜振蕩。
(6) 油膜振蕩時(shí), 振動(dòng)的波形發(fā)生畸變, 在工頻的基波上疊加了低頻成分, 有時(shí)低頻分量占主導(dǎo)地位, 低頻振動(dòng)的幅值不穩(wěn), 軸心軌跡發(fā)散。
(7) 油膜振蕩的發(fā)生和消失具有突然性, 并具有慣性效應(yīng), 即升速時(shí)產(chǎn)生振蕩的轉(zhuǎn)速比降速時(shí)振蕩消失的轉(zhuǎn)速要大。
(8) 油膜振蕩劇烈時(shí), 隨著油膜的破壞, 振蕩停, 油膜恢復(fù)后, 振蕩再次發(fā)生, 這樣持續(xù)下去, 軸頸與軸承不斷碰摩, 產(chǎn)生撞擊聲, 軸瓦內(nèi)油膜壓力有較大波動(dòng)。
(9) 油膜振蕩對轉(zhuǎn)速和油溫的變化較敏感, 一般當(dāng)旋轉(zhuǎn)機(jī)械發(fā)生油膜振蕩時(shí), 隨著轉(zhuǎn)速的增加, 振動(dòng)不下降, 隨著轉(zhuǎn)速的降低, 振動(dòng)也不立即消失, 稱為滯后現(xiàn)象; 提***進(jìn)油溫度, 振動(dòng)一般有所降低。
2.2.2 軸承巴氏合金碎裂和燒蝕軸承巴氏合金碎裂是指由于某種原因造成巴氏合金軸瓦表面損壞, 如坑斑、開裂、剝落等。當(dāng)巴氏合金軸瓦發(fā)生剝落, 潤滑油在軸承中循環(huán)流動(dòng)必然攜
帶著由于剝落而產(chǎn)生的巴氏合金碎片。導(dǎo)致軸承巴氏合金碎裂的原因有[3]:
(1) 固體作用———油膜與軸頸碰摩引起的碰撞及摩擦, 以及潤滑油中所含雜質(zhì)(磨粒)引起的磨損;
(2) 液體作用———油膜壓力的交變引起的疲勞破壞;
(3) 氣體作用———潤滑膜中含有氣泡所引起的氣蝕破壞。
軸承巴氏合金燒蝕是指由于某種原因造成軸頸與軸瓦發(fā)生摩擦, 使軸瓦局部溫度偏***, 巴氏合金氧化變質(zhì), 轉(zhuǎn)子發(fā)生嚴(yán)重的熱彎曲、熱變形, 甚至抱軸。
軸承與軸頸碰摩和巴氏合金碎裂發(fā)展到晚期都將導(dǎo)致軸承巴氏合金燒蝕。此外, 潤滑不良也能導(dǎo)致軸承巴氏合金燒蝕。
當(dāng)發(fā)生軸承與軸頸碰摩時(shí), 其油膜就會(huì)被破壞。
摩擦使軸瓦巴氏合金局部溫度偏***, 從而致使巴氏合金燒蝕, 由此引起的軸瓦和軸頸的熱脹差, 進(jìn)一步重軸瓦與軸頸的摩擦, 形成惡性循環(huán), 使巴氏合金軸瓦燒蝕不斷加重。軸瓦巴氏合金碎裂的落物還容易阻塞油孔, 使供油不足而導(dǎo)致油膜破裂。如果供油油壓過低, 正常的油膜難以建立, 會(huì)使油膜破裂; 如果供油油溫過***, 不僅會(huì)使軸承過熱發(fā)生熱變形, 同時(shí)還會(huì)使油粘度下降, 油膜變薄而導(dǎo)致油膜破裂。軸承巴氏合金燒蝕的***常見的原因是斷油。斷油將使軸頸和軸瓦直接進(jìn)入干摩擦狀態(tài), 并且沒有潤滑油將摩擦熱量帶走, 從而使軸承巴氏合金迅速燒蝕。
根據(jù)前文滑動(dòng)軸承的工作原理, 當(dāng)軸承巴氏合金出現(xiàn)缺陷并且軸頸在損傷表面轉(zhuǎn)動(dòng)時(shí), 便會(huì)產(chǎn)生一種交變的激振力。由于軸頸表面的損傷形狀是不規(guī)則的, 所以激振力產(chǎn)生的振動(dòng)將是有多種頻率成分組成的隨機(jī)振動(dòng)。從軸承滑動(dòng)表面狀況產(chǎn)生振動(dòng)的機(jī)理可知, 軸承滑動(dòng)表面損傷的形態(tài)和軸的旋轉(zhuǎn)速度, 決定了激振力的頻率; 軸承和外殼, 決定了振動(dòng)系統(tǒng)的傳遞特性。因此, 振動(dòng)系統(tǒng)的***終振動(dòng)頻率, 由上述二者共同決定。也就是說, 軸承異常所引起的振動(dòng), 其頻率成分由軸的旋轉(zhuǎn)速度、損傷部分的形態(tài)及軸承與外殼振動(dòng)系統(tǒng)的傳遞特性所決定, 將表現(xiàn)為非線性彈簧性質(zhì)的振動(dòng)。軸向非線性伴生振動(dòng)頻率為軸的旋轉(zhuǎn)頻率fr, 分?jǐn)?shù)諧波12fr, 13fr, ?及其***次諧波2fr, 3fr?; 而徑向非線性伴生振動(dòng)是nfr的各次諧波及fr的分?jǐn)?shù)諧波成分。
3 故障實(shí)例
某渦輪增壓器工作流程如圖2 所示。渦輪增壓器的壓氣機(jī)和渦輪都為離心式旋轉(zhuǎn)機(jī)械, 轉(zhuǎn)軸安裝在3 個(gè)滑動(dòng)軸承上。其工作原理為: ***溫燃?xì)馔苿?dòng)渦輪旋轉(zhuǎn), 渦輪帶動(dòng)壓氣機(jī)做功, 使壓氣機(jī)進(jìn)口的常壓空氣變成***壓氣體, ***壓氣體進(jìn)入燃燒室與燃油混合后燃燒, 獲得的***溫燃?xì)庠倭魅霚u輪中做功。如此往復(fù)循環(huán)。

在該渦輪增壓器試驗(yàn)中, 為了測量其振動(dòng)大小,在壓氣機(jī)垂直和壓氣機(jī)水平兩個(gè)位置分別安裝了ENDEVOC 加速度振動(dòng)傳感器, 試驗(yàn)中規(guī)定的振動(dòng)報(bào)警值為5g。該試驗(yàn)振動(dòng)測試系統(tǒng)簡圖如圖3 所示。
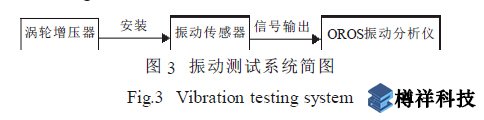
試驗(yàn)從低轉(zhuǎn)速逐漸向***轉(zhuǎn)速推進(jìn), 已成功運(yùn)行了幾次。在***后一次試驗(yàn)中, 試驗(yàn)件在30 000 r/min前, 振動(dòng)波形及頻譜圖一切正常, 在從30 000 r/min推到40 000 r/min 的過程中, 增壓器的振動(dòng)幅值突然增加, 頻譜圖上突然出現(xiàn)了豐富的次諧波以及大幅值的***頻振動(dòng)。振動(dòng)頻譜如圖4~圖7 所示。圖中,上面曲線為垂直位置振動(dòng), 下面曲線為水平位置振動(dòng)。

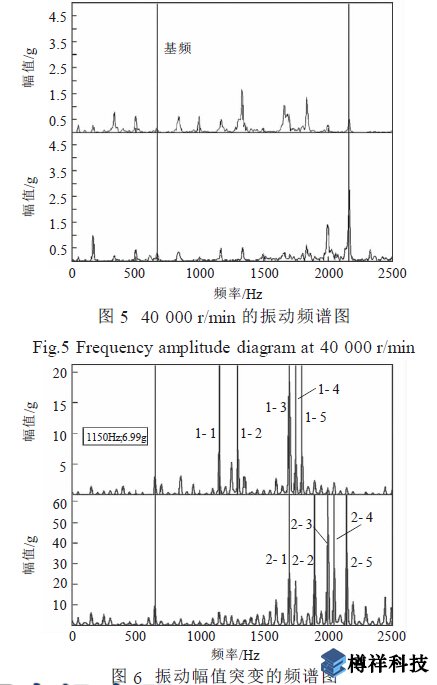
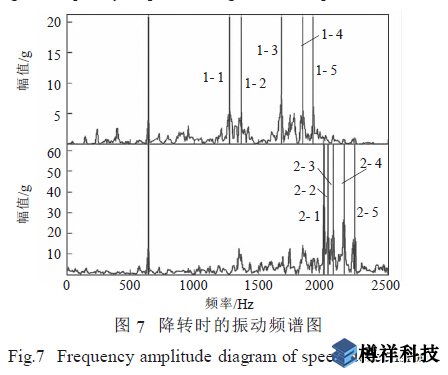
圖4 為穩(wěn)定在30 000 r/min 的振動(dòng)頻譜圖, 圖5為以前試驗(yàn)中穩(wěn)定在40 000 r/min 的振動(dòng)頻譜圖。在這兩幅圖中, 都有低于基頻的頻率成分出現(xiàn), 似乎出現(xiàn)了次諧波振動(dòng)。經(jīng)分析發(fā)現(xiàn), 圖中低于基頻的幅值都是由工頻干擾信號引起的, 不是異常振動(dòng)信號。圖4、圖5 中, 從0 Hz~2 500 Hz 的頻帶內(nèi)振動(dòng)幅值都不超過4g, 沒有中***頻峰值群出現(xiàn), 基頻振動(dòng)幅小于2g。這說明在這兩個(gè)狀態(tài)下, 渦輪增壓器轉(zhuǎn)子系統(tǒng)運(yùn)行正常。
圖6 為從30 000 r/min 推到40 000 r/min 的上升過程中達(dá)到39 000 r/min 時(shí)振動(dòng)幅值頻譜發(fā)生突變的頻譜圖。從圖中可以看出, 在1 100 Hz~2 100Hz 之間出現(xiàn)了峰值群, ******振動(dòng)幅值達(dá)57.44g, 基頻振動(dòng)幅值也超過了10g。這表明此時(shí)渦輪增壓器的機(jī)械運(yùn)行狀態(tài)發(fā)生突變, 已經(jīng)出現(xiàn)了故障。圖7 為報(bào)警后試驗(yàn)件迅速降轉(zhuǎn)時(shí)的振動(dòng)頻譜圖, 圖中中***頻的大幅振動(dòng)峰群仍然存在, 基頻嚴(yán)重超限, 已經(jīng)達(dá)到了14.45g, 渦輪增壓器已經(jīng)不能正常運(yùn)行。
圖6 中的部分峰值幅值如表1 所示, 從中可以看出圖6 中有明顯的倍頻成分和分?jǐn)?shù)成分諧波。根據(jù)前文的討論, 可認(rèn)為渦輪增壓器的軸承出現(xiàn)了巴氏合金碎裂或燒蝕故障, 圖6 中該峰群的中心頻率與軸承外圈及其外殼形成的振動(dòng)系統(tǒng)的一階徑向固有振動(dòng)有關(guān)。
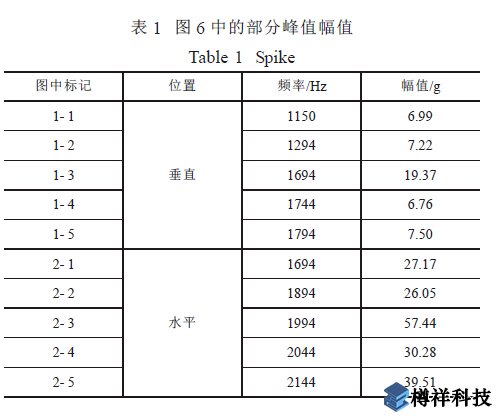
經(jīng)分解檢查發(fā)現(xiàn): 試驗(yàn)件渦輪端的軸承已經(jīng)損壞, 軸承全部燒黑, 軸頸出現(xiàn)劃痕并且變藍(lán)。從滑動(dòng)軸承燒蝕的跡象看, 是短時(shí)間內(nèi)軸承達(dá)到了很***的溫度, 導(dǎo)致軸承燒蝕、軸頸燒藍(lán)。
4 故障原因分析
可能造成渦輪增壓器渦輪端軸承超溫的主要原
因有兩種:
(1) 由于密封不嚴(yán), ***溫燃?xì)膺M(jìn)入軸承腔內(nèi), 導(dǎo)致超溫。
(2) 由于供油油壓過低, 正常的油膜難以建立,使油膜破裂造成軸頸與軸瓦發(fā)生干摩擦; 同時(shí), 潤滑油流量不夠, 不能將摩擦熱量帶走, 所以在轉(zhuǎn)子轉(zhuǎn)速上升過程中使軸承巴氏合金迅速燒蝕。
試驗(yàn)后的分析、檢查發(fā)現(xiàn), 渦輪端軸承的密封脹圈工作正常, 基本排除了密封不嚴(yán)導(dǎo)致***溫燃?xì)膺M(jìn)入軸承腔內(nèi)的故障原因。
試驗(yàn)中所采用的滑油牌號為CD40, 油箱中的油溫為14℃, 滑油泵出口壓力為0.5 MPa, 滑油泵出口壓力監(jiān)視點(diǎn)距增壓器進(jìn)口管路長約3 m。通過計(jì)算可知, 因滑油溫度低, 其運(yùn)動(dòng)粘度***達(dá)3 000 mm2/s,從而使得滑油壓力損失達(dá)0.3 MPa; 與此相對應(yīng)的是, 試驗(yàn)要求增壓器進(jìn)口滑油壓力0.3~0.4 MPa。
因此, 滑動(dòng)軸承燒蝕的主要原因應(yīng)是: 進(jìn)口滑油溫度低, 壓力損失大, 致使供油油壓過低, 正常的油膜難以建立; 同時(shí), 潤滑油流量不夠, 不能將摩擦熱量帶走, 致使軸承巴氏合金迅速燒蝕。故障現(xiàn)象表現(xiàn)為振動(dòng)狀態(tài)立刻改變。
5 解決方法
根據(jù)故障分析結(jié)果, 更改了渦輪增壓器滑油供給方式。主要是減短油箱到渦輪增壓器滑油進(jìn)口之管路的長度, 降低流阻損失[4], 同時(shí)提***油泵供油壓力, 即提***供油量。采取這些措施后, 在其后的試驗(yàn)中, 振動(dòng)幅值得到了很好的控制, 中***段頻率成分比較干凈, 沒有明顯的分?jǐn)?shù)頻率和倍頻。這說明當(dāng)滑油流量滿足渦輪增壓器軸承的要求時(shí), 其振動(dòng)幅值較小, 機(jī)械運(yùn)行狀態(tài)良好。
6 結(jié)論
根據(jù)理論分析及實(shí)踐中獲得的軸承故障經(jīng)驗(yàn),當(dāng)滑動(dòng)軸承出現(xiàn)故障后, 在振動(dòng)信號上有明顯的特征, 即: 出現(xiàn)一簇中***頻大幅振動(dòng)峰群; 出現(xiàn)大量的次諧波振動(dòng)以及豐富的倍頻幅值; 基頻振動(dòng)幅值上升。這些特征將為軸承故障診斷提供強(qiáng)有力的幫助。
通過故障分析, 使我們采取了正確的解決措施, 有效地杜絕了此類故障的再次發(fā)生。